Learn How to Get the Most Out of Your Supply Chain Management System
Introduction
The supply chain is a complex network of companies that interact with one another in order to produce a product or service. It is a key component of any business, and if it isn’t managed properly, it can have a devastating impact on a company’s bottom line. In fact, if you want to make sure that you’re always getting the best possible service from your suppliers, then you need to make sure that you have the right supply chain management system in place.
With a good supply chain management system, you can ensure that you get the best possible service from your suppliers, and that your business gets the best possible service from your customers. This means that your business will be more profitable, more efficient, and more productive. It will also mean that you can spend less time managing your business, and more time doing what you do best: growing your business.
In this article, I will be providing you with a comprehensive guide on the topic of supply chain management.
You will learn how to properly plan your supply chain, what it is, why it’s important, and how it works.
You will also learn how to identify the major players involved, what their roles are, and what the best practices are.
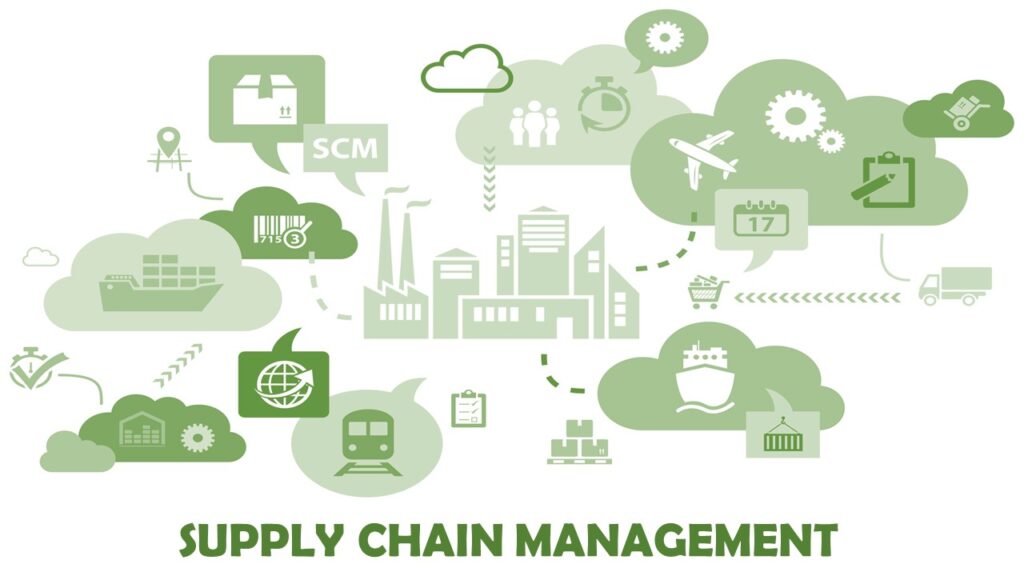
Supply Chain Management
A supply chain is a network of suppliers and customers that creates value through the exchange of goods and services. Supply chains help to manage the flow of products and services through the entire supply chain.
A supply chain is a complex system with many interacting parts, such as suppliers, manufacturers, wholesalers, distributors, retailers, consumers, and the environment. The complexity of supply chains is compounded by the fact that many of these parts are not directly controlled by the end user.
Supply chains can be categorized into two major types: vertical and horizontal.
Vertical supply chains have one or more levels of management at each stage of the process, and a single buyer.
Horizontal supply chains are comprised of multiple buyers at each level of the process, and no single level of management.
The Importance of Supply Chain Management
The supply chain is an essential part of every business. Without a good supply chain, a company will not be able to survive. The supply chain is a complex web of different parties.
It is the responsibility of the supply chain manager to ensure that all the pieces are in place for the company to be successful.
A company can’t rely on one supplier alone. They need to be able to trust their suppliers and know that they will be there when needed. There needs to be a partnership between the customer and the supplier. When it comes to the supply chain, it is critical that there is communication between all parties. If a problem arises, everyone needs to know about it so that they can work together to fix it.
The supply chain needs to be streamlined so that the entire process is efficient. It is important that the supply chain manager has control of the flow of the products and the materials.
Supply Chain Management Process
The supply chain management process is what makes it possible for a company to function.
The first step in the supply chain process is the planning stage. This is when companies decide what they are going to produce, how much they are going to produce and where they are going to produce it.
After the planning stage, the next step is production. Production is the process of actually producing what has been planned. It is also when companies make decisions about the cost, quality, time and place of production.
Once the planning and production stages are complete, the final step is distribution or delivery. This is the time when companies deliver their products to the customer.
Step 1: Planning
The planning stage is when a company decides what they are going to produce, how much they are going to produce, and where they are going to produce it. Companies will first make a decision on what they are going to produce. They can make this decision based on their customers, their employees, or some other external factor.
Companies often base their decisions on the market. This is because many companies see their market as a constant that they need to keep up with. A company might make the decision to focus on a certain market because of their current financial situation. For example, a company might be in financial trouble and decide to produce more of one of its products in order to increase sales.
Next, a company will decide how much of the product they are going to produce. Companies usually decide how much they are going to produce based on what their customer wants. However, a company might decide how much they are going to produce based on what they are currently producing. For example, if a company is currently producing a lot of a certain product, then they might decide to increase production of that product.
Finally, a company will decide where they are going to produce the product. A company might decide that it is going to produce the product in their own facility, or they might decide that they are going to outsource the production of the product.
Step 2: Production
Once a company decides what they are going to produce, they must then decide how much of the product they are going to produce. A company might choose to produce a certain amount of a product because of the market they are trying to appeal to. This is because if a company wants to appeal to a particular market, then they might need to produce a certain amount of the product in order to compete in that market.
A company might also decide how much they are going to produce based on their current financial situation. For example, if a company has a large amount of debt, they might decide to reduce the amount of product they are producing in order to pay off the debt. Next, a company will decide where it is going to produce the product. A company might decide to produce the product in its own facility or it might decide to outsource production.
Step 3: Distribution or Delivery
Once a company decides what it is going to produce, it must then decide how it is going to deliver the product. A company might decide to deliver the product itself. This might be done in person, or by a courier service. A company might also decide to sell the product over the internet, or through other mediums.
Planning the Supply Chain
In order to plan your supply chain, you must first know what your demand is. This will help you determine the amount of inventory you will need to maintain. Once you have determined what your demand is, you can identify the suppliers you will need to work with. You must also identify the best practices and processes that will help you to run a smooth supply chain.
A successful supply chain is one that allows you to maximize the profit of your company, while minimizing your costs.
The following are some questions that will help you determine your demand. How much do you sell? What is the average sales volume per day, week, month or year? Do you sell only one product or do you sell multiple products? Do you sell to customers in the United States, or overseas? Are your customers seasonal? What are the fluctuations in your customer base? What is the seasonality of your business?
If you are a small business, you may not be able to answer all these questions. However, you can use the following questions to determine your demand: How many products do you plan to make? How many products do you plan to sell? How many products do you expect to sell each day?
Identifying the Players
In order to properly manage your supply chain, you must identify all of the different players involved. You must know what their roles are and how they interact with each other.
Who are the players in supply chain management?
The players in supply chain management include the buyer, the seller, and the shipper. The buyer, also known as the buyer’s agent, is responsible for acquiring products, services, and/or equipment. The seller is the supplier of goods and services. The shipper is the person who ships the goods and services from the seller to the buyer.
Supply chain management involves the planning, execution, and control of the flow of goods and services from the supplier to the buyer. The key to success in supply chain management is the ability to work well with people from all three parties.
The buyer is responsible for the selection and acquisition of products, services, and/or equipment. The buyer must know what they want, how much it costs, and where to find it.
The seller is the supplier of the product or service. The seller is responsible for getting the product or service to the buyer. The seller can be the manufacturer, distributor, retailer, or any other type of seller.
The shipper is the person who ships the goods and services from the seller to the buyer. The shipper is responsible for the packaging, delivery, and handling of the goods and services.
Identifying the Role of the Supply Chain Manager
The supply chain manager is the person who is in charge of managing the supply chain. The supply chain manager is the person who will ensure that all of the different parties are working together to ensure a successful supply chain.
Supply chain management is an important function in any business. Without a good supply chain manager, your business will be left behind by competitors. A great supply chain manager will make sure that you have what you need when you need it. This means that you can get things done more efficiently, and your business will grow.
A good supply chain manager will also help you get the best prices. They will negotiate with suppliers to get the best price for your products. This is because they know how to negotiate and understand how to save money for you.
The good news is that a good supply chain manager doesn’t cost much. You just need to hire one who has experience in this field. The most important thing you need to look for in a supply chain manager is someone who can communicate well with your customers. This is because they are the ones who will be buying your products.
A good supply chain manager will also be able to manage inventory. This means that you won’t be left with a surplus of inventory. You will always have enough of what you need.
Finally, a good supply chain manager will make sure that you get the right things on time. They will make sure that your customers get their orders on time, and that they get what they ordered.
Identifying the Roles of the Different Parties
The supply chain is made up of three main components:
- The demand side – where the customer buys the product.
- The supply side – where the manufacturer produces the product.
- The logistics – where the products are moved from the suppliers to the customer.
Each of these three components plays a crucial role in the supply chain.
The demand side is what generates the need for the product, the supply side creates the product, and the logistics makes sure that the product reaches the right place at the right time.
Identifying the Roles of the Demand Side
The demand side is where the customer buys the product. The demand side includes the customers, the retailers, and the wholesalers. The customer is the ultimate consumer of the product. A customer can be a retailer or a wholesaler. A retailer is a person who sells products to a customer. Wholesalers sell products to retailers at a lower price than what they sell to the public. Retailers are the middleman who sells products to the customer.
The demand side also includes the customers and the manufacturers. The demand side is the person who wants to buy the product.
Identifying the Roles of the Supply Side
The supply side is where the manufacturer produces the product. The supply side includes the manufacturers, the distributors, and the wholesalers. The supply side is the person who makes the product.
The manufacturer produces the product. The manufacturer includes the people who work at the factory, the workers who make the product, the engineers who design the products, and the managers who oversee the employees. The distributor receives the product from the manufacturer. The distributor is the middle man between the manufacturer and the consumer. The distributor is a company that sells products to stores or other businesses.
Identifying the Roles of the Logistics
The logistics are where the products are moved from the suppliers to the customer. The logistics include the carriers, the transportation companies, the warehouses, the distribution centers, and the fulfillment centers. The logistics is the person who transports the product from the suppliers to the customer.
The logistics company is one of the most important people in the business. They can make or break your business. You should be very careful when choosing a logistics company. There are many things to consider when selecting a logistics company.
There are many logistics companies out there that can help you ship products. The best thing to do is to research different logistics companies and compare them based on their shipping policies, shipping methods, costs, and customer service.
You want to find the best logistics company for your needs. You don’t want to pay for something that you are not getting.
What Is a Logistics Company?
A logistics company is an organization that ships goods from one location to another. A logistics company takes products from the suppliers to the customers. The logistics companies handle all aspects of the shipments, such as:
- Pick-up and drop off.
- Storage of the products until they are delivered to the customer.
- The billing and payment of the goods.
- Shipping the products.
A logistics company does not deliver the products to the customers, but rather provides the transportation services to get the products to the customer. Most logistics companies are small businesses that provide services to other businesses or individuals. The services provided by a logistics company can vary depending on what is being shipped. Some logistics companies only handle small shipments of items while others handle large quantities of items.
Identifying the Roles of the Customer
The customer is the person who buys the product. The customer includes the retailers, the wholesalers, and the end-users.
The customer is also called the end-user. This is because there are many different ways to consume a product. It can be consumed by the consumer, by a retailer, by a wholesaler, or by an end-user. The retailer is the person or company that is the primary purchaser of the product from the manufacturer. The retailer includes the retail stores, the wholesale distributors, and the independent retailers.
FAQ
Why do we need a supply chain?
A supply chain has many moving parts. There are the suppliers, who make the product or service. Then there are the buyers, who purchase the product. Next, there is the distribution center, which ships the product to the retailer. Finally, there are the customers, who use the product.
So, what’s the point? Why do we need a supply chain?
It’s all about efficiency. If you’re a manufacturer, you’ll want to create a supply chain that’s efficient so that you can produce more products and services. If you’re a retailer, you’ll want a supply chain that’s efficient so that you can sell your products faster.
What does this have to do with creativity?
Creativity is about being more effective. The more you can use a supply chain to help you be more efficient, the more you can be creative.
For example, you could use a supply chain to create more sales. You can create an efficient supply chain by getting in touch with retailers and distributors to learn what they want and what they need. Then, you can create new products or services to meet those needs.
You can also use a supply chain to be more effective at customer service. For example, if you’re a manufacturer, you can use a supply chain to deliver products quickly and efficiently. This allows you to answer questions and solve problems for your customers.
Finally, you can use a supply chain to be more effective at marketing. For example, you can use a supply chain to get the word out about your product or service. You can create a supply chain that delivers your product or service to the right people at the right time. This will help you reach more customers and increase sales.
What is a supply chain?
A supply chain is a system that provides a constant flow of products and services to customers. It’s a complex web of people, processes, and technologies that connect the company to its customers. It’s a complex web of people, processes, and technologies that connect the company to its customers.
Supply chains are vital to the success of any business. They enable companies to grow and prosper by providing them with the ability to produce, distribute, and sell their products and services. Supply chains help companies to do this by providing them with access to raw materials, suppliers, and distributors.
A supply chain is the lifeblood of any business. It’s the backbone of any company that sells products or services to the public. Companies that don’t have a supply chain will be out of business within a few years.
How do you run a supply chain?
A supply chain is not a single line or one product, but rather a series of steps and activities that move a product from its origin to its destination. Supply chain management involves the planning, scheduling, and coordination of the various steps and activities that make up a supply chain.
The goal of supply chain management is to ensure that the flow of goods is smooth and efficient. It is not as simple as it sounds. There are many different types of supply chains, and each has its own unique set of challenges. A supply chain may involve the flow of products from an agricultural field to a manufacturing facility, from a manufacturing facility to a retail outlet, or from a retailer to a customer.
There are many different types of supply chains. A supply chain may involve the flow of products from an agricultural field to a manufacturing facility, from a manufacturing facility to a retail outlet, or from a retailer to a customer.
A supply chain can be broken down into several key components:
- Planning
- Scheduling
- Coordination
- Monitoring
- Control
- Reporting
The first step in any supply chain is planning. This is the process of determining where the product is going and how it will get there.
After planning, the next step is scheduling. This involves planning the order in which the steps of the supply chain will be carried out.
The third component of a supply chain is coordination. Coordination involves ensuring that all of the steps of the supply chain are carried out on time.
The fourth component of a supply chain is monitoring. Monitoring involves making sure that everything is going smoothly. It is the process of checking the status of the supply chain and identifying any problems or issues that may arise.
The fifth component of a supply chain is control. Control involves making sure that each step of the supply chain is being carried out correctly.
The sixth component of a supply chain is reporting. Reporting involves taking the information gathered by monitoring and using it to make decisions about the supply chain.
Supply Chain Management Software
Supply Chain Management (SCM) software is designed to help manufacturers and distributors manage the entire flow of products from the time they are created or sourced, through the manufacturing process, to when they reach the final consumer.
The role of a good supply chain management software is to track inventory, automate procurement and production processes, manage deliveries, orders and customer service. Most importantly, it is a good tool for monitoring the movement of goods through the manufacturing and distribution process.
Today, most manufacturers use some sort of SCM software to organize their supply chains and make sure that all the activities related to the flow of goods are done in a smooth manner. It helps in reducing costs, improving efficiency and streamlining operations.
How to build a supply chain?
A supply chain is a collection of resources that a company uses to produce a product or service. It is a chain of activities that starts with raw materials and ends with the finished product.
The concept of a supply chain is an extension of the idea of production. A company creates a product, which then needs to be produced by others before it can be sold to consumers. This is the essence of a supply chain.
In this case, the raw materials are the inputs that go into the production process. These are the things that the company buys from other suppliers. The inputs are the raw materials that the company uses to create the final product.
For example, a company might buy a raw material such as wood from a supplier. This raw material is used to create a wooden cabinet. Once the raw material is purchased, the company must then pay someone else to build the cabinet. This person may be a cabinet maker, a carpenter, or a construction worker. Once the cabinet is finished, the company must then sell it to a consumer.
So, a supply chain is a chain of activities that starts with raw materials and ends with the finished product. It is a collection of resources that a company uses to produce a product or service. It is a chain of activities that starts with raw materials and ends with the finished product.
Why it’s important to have a supply chain
When you’re creating a product, you need to make sure that the product you’re making will be able to meet the demands of your customers. You want to make sure that the product you’re creating is going to be something that your customers will want to buy.
If you don’t have a supply chain in place, then you won’t know if your product is going to be able to meet the demands of your customers. Your customers will be out of luck if they can’t find the product that they’ve been looking for.
So, you need to make sure that your product has a supply chain in place. If you don’t, then you’ll be creating a product that’s going to be out of stock and not be able to meet the demand of your customers.
A supply chain is the process of making sure that your product is going to be available to your customers. It’s also the process of making sure that your product is going to be able to meet the demands of your customers.
There are a lot of different parts of a supply chain.
The first step of your supply chain is going to be to make sure that you’ve got the right product. You need to make sure that you’ve got the right product that you’re going to be able to sell to your customers.
The second step of your supply chain is going to be to make sure that you’ve got the right distribution. You need to make sure that you’ve got the right distribution because you don’t want to be creating a product that’s going to be out of stock and not be able to meet the demands of your customers.
The third step of your supply chain is going to be to make sure that you’ve got the right marketing. You need to make sure that you’ve got the right sales because you don’t want to be creating a product that’s going to be sitting on the shelf and just not meeting the demands of your customers.
What is a supply chain manager?
A supply chain manager is responsible for managing the flow of goods from their point of origin to their point of use. They plan and coordinate the movement of materials and products to the customer. A supply chain manager also ensures that these materials are delivered on time and in the right quantities.
A supply chain manager is responsible for monitoring the flow of materials and products through the supply chain. This means that they must monitor the entire process, from the manufacturing of the product to its delivery to the customer.
A supply chain manager may also be responsible for coordinating the efforts of other members of the supply chain team. For example, a supply chain manager may be in charge of making sure that the transportation team is able to deliver the goods to the customer on time and in the right quantities.
A supply chain manager may also be responsible for ensuring that the customer is satisfied with the product. This includes making sure that the customer receives the right product at the right time.
A supply chain manager must be able to communicate effectively with all members of the supply chain team. They must be able to explain the process to their team and ensure that they understand the process. They must also be able to relay information to their team, so they can perform their duties efficiently.
What is a supply chain analyst?
A supply chain analyst is a person who works with a business to track and monitor their supply chain. They are responsible for monitoring the movement of products throughout the supply chain. This includes tracking the origin, movement, and delivery of a product.
A supply chain analyst will be able to help a business identify problems or issues in the supply chain and then work to resolve those issues.
Supply chain analysts are also responsible for monitoring the movement of products from one company to another. They will be able to track and monitor the movement of the product from the manufacturer to the distributor to the retailer to the consumer.
What is a supply chain coordinator?
A supply chain coordinator is a person who manages the flow of materials, equipment, and people throughout the supply chain. It is an integral part of the logistics management process.
The supply chain coordinator is responsible for the organization, management, and coordination of all the elements of the supply chain. The goal of the supply chain coordinator is to ensure that all the resources are used efficiently and effectively.
A supply chain coordinator may be involved in the planning, design, implementation, and management of the production process. It is a very important job because it helps companies maintain a steady flow of materials and equipment throughout the supply chain.
The supply chain coordinator is the central point of communication between the supplier, the buyer, and the customer. It is the middle man, and it ensures that the necessary materials and equipment are available when needed.
The supply chain coordinator makes sure that all the necessary resources and equipment are available and in the right place at the right time. This is done by keeping up-to-date records of the materials and equipment in the company’s inventory.
The supply chain coordinator also makes sure that the company has enough of the materials and equipment to meet its customers’ needs. The coordinator must be familiar with the products being sold and the customers’ needs.
The supply chain coordinator is responsible for making sure that the company meets the customers’ expectations. The coordinator must be able to communicate effectively and solve problems that arise along the way.
Final Words
In conclusion, if you want to be successful in your supply chain, you need to have a comprehensive plan that will help you manage your supply chain in the best possible way. To start with, you need to know exactly what you want from your supplier. You should be able to describe your needs clearly and give your supplier the information that they need to fulfil them. You should also have a detailed understanding of what your supplier does and what they can do for you.
Disclosure: Some of the links to products on this blog are affiliate links (paid link). It simply means, at no additional cost to you, I’ll earn a commission if you click through and buy any product.